
86 17344894490
service@chalcoaluminum.com
차량 제조에서 압출 알루미늄 프로파일 구조 부품
정보에 따르면, 유럽 기관차 및 차량 제조업체의 기존 주문의 약 60 %는 알루미늄 몸체가있는 차량입니다. 20 년 전, 그러한 주문은 2 % - 3 %에 불과했습니다. 이제 알루미늄 구조는 얼음, tgv-2n, etr460, etr500, Talgo Hotel 기차 및 기타 고속 열차뿐만 아니라 많은 교외 및 도시 철도 운송 차량에 적용되었습니다.
압출 알루미늄 프로파일 구조 부품의 채택은 1970 년대 초에 시작되었습니다. 그 당시 알루미늄 프로파일 적용의 과학 기술 발전으로 인해 필요한 모양과 크기에 따라 알루미늄 부품을 만들 수있었습니다. 이 알루미늄 구성 요소는 영국의 apt 열차의 틸팅 차체에 적용되었습니다. 그러나 그 당시 압출 알루미늄 부품의 적용은 큰 이점을 얻지 못했고, 즉 높은 재료 가격은 제조 작업량의 감소를 보상하지 못했습니다. 당시 대형 구조 부품을 사용하면 차체의 생산 작업량이 40 % 감소하고 26m 길이 차체의 중량이 7.5t로 감소한 반면 26m 길이의 강철 차체의 중량은 11T였습니다. 1970 년대에 철도 부서는 차량의 전체 서비스 수명 (구매 비용 + 운영 및 유지 보수 비용)의 총 비용 계산에 더 많은 관심을 기울였습니다. 그들은 열차 견인 에너지의 소비가 동일한 수준으로 유지되어야한다는 것을 깨달았고, 이는 주로 롤링 스톡의 자체 무게에 달려 있습니다.
나중에, 1980 년대 중반에 달성 된 몇 가지 새로운 기술 및 기술 조치, 예를 들어 횡단 고정의 필요성을 최소한으로 줄인 이중층 쉘의 대형 구조 부품의 압출 방법의 채택과 같은 몇 가지 새로운 기술 및 기술 조치는 철강 차량에 비해 50 % 감소한 차량 알루미늄 본체의 생산 시간을 더욱 단축했습니다. 그리고 기존의 방법에 따라 이층 실린더 몸체를 만들 수 있었고, 창문 구멍을 개봉 한 후 용접 작업은 모두 로봇 기술 및 장비를 사용하여 부분적으로 만 통일 된 기술 작업 과정에서 완료됩니다.
이제 철도 부서가 초기 제조 비용과 향후 운영 비용을 줄이기 위해 신차 개발에 대한 참여를 점진적으로 줄이고 구매 정책을 시행하면 제조업체는 가입자의 기술 요구 사항을 충족시키고 시장 개발 추세에 적응하기 위해 새로운 구조와 재료를 채택 할 자유가 커집니다. 압출 알루미늄 프로파일 구조 부품 은 또한 차량 구조에 대한 엄격한 요구 사항을 충족시키는 데 다른 장점이 있습니다. 예를 들어, 이중층 쉘 압출 구조의 강성은 고속 열차가 충족 될 때 생성되는 공기 역학적 충격이 특별한 충격 강도를 갖도록 보장 할 수 있습니다. 이 구조를 가진 차체의 또 다른 중요한 특징은 큰 세로 강성입니다. 세로 강성과 횡방향 강성의 비율은 70 : 30에 도달 할 수 있으며 강철 차체의 비율은 40 : 60입니다. 또한 알루미늄 프로파일은 필러를 사용하지 않고 많은 수동 작업없이 우수한 외부 모양의 요구 사항을 충족시킬 수 있습니다. 예를 들어, 독일 연방 철도의 일부 모델의 경우 필러가 사용되지 않기 때문에 계산 후 페인트 코팅과 함께 자체 무게는 500kg이 될 수 있습니다.
압출 알루미늄 프로파일 구조 부품을 사용하면 차량 제조업체가 복잡한 작업에 직면하게됩니다. 그들은 노동과 재료 가격 사이의 균형을 찾아야하며, 디자이너가이 균형을 이루기 위해 노력하도록해야합니다. 재료는 전체 개념에서 단지 하나의 요소 일 뿐이라는 것을 분명히해야합니다. 채택 된 생산 공정 및 기술 공정은 기업의 생산 능력에 부합하고 투자와 균형을 이루도록 정교하게 공식화되어야합니다.
예를 들어, 대부분의 기계 제조 회사의 경우 생산 수단의 매장량을 최소화하는 것이 최우선 과제입니다. 디자이너가 재료 및 공정을 선택하는 것은 이에 큰 영향을 미칩니다. ABB는 매주 알루미늄 본체로 8 대의 차량을 생산할 수있는 생산 라인을 갖추고있어 재료 보관의 총 비용을 8 % 절감합니다. 그러나이 균형은 재료 사용으로 인한 기술 프로세스의 변화로 인해 쉽게 파괴됩니다. 예를 들어, 용접에서 본딩으로의 전환이 접합 경화에 필요한 상당한 시간을 보상하기 위해 더 많은 일일 매장량을 필요로 할 때.
롤링 스톡 제조를위한 알루미늄 프로파일의 또 다른 선도적 인 공급 업체는 독일의 VAW 회사입니다. 회사의 지도자들은 차량 구조의 표준화와 모듈 설계 방법의 채택에 큰 발전 추세가 있음을 예견하고 (이러한 추세는 시장 수요로 인해 강화되었으므로 제조업체의 지원을 받음), 독일의 지역 철도 운송의 지역화에 대한 시장 수요를 고려할 때, 일부 민간 기업은 개별 주문자의 요구 사항을 더 많이 충족시키기 위해 표준화 된 모듈 구조를 사용하는 데 더 많은주의를 기울일 것입니다. 현재 다양한 유럽 기관차 및 차량 제조업체는 많은 디자인 아이디어를 가지고 있으며 이러한 아이디어는 모듈 디자인을 기반으로합니다. 표준화 및 모듈화로의 이러한 전환은 생산자와 사용자 모두에게 유익합니다. 차량 제조에서 알루미늄 프로파일의 사용의 확장은 자동 용접의 광범위한 사용으로 인해 생산주기를 크게 줄일 것입니다.
용접 된 알루미늄 차체 차량은 높은 충격 하중 저항을 가지며 이는 운전 안전 향상에 도움이된다는 것도 분명합니다. ABB는 알루미늄 구조물의 파괴 테스트를 조직하고 수행하기 위해 1 백만 파운드를 투자했으며 만족스럽고 더 중요한 것은 예상되는 테스트 결과를 얻었습니다. 이 회사는 또한 사고 차량의 고장 방법을 수리하는 데 귀중한 실제 경험을 축적했습니다. 1994 년 초, 프랑스의 GEC Alstom이 주문한 tgv-2n 열차의 더블 데크 승용차 테스트 샘플에 대한 손상 테스트는 충격력이 250t가 될 때 8mj의 흡수 된 충격 에너지로 인해 구조물이 총 80cm 동안 압출되었고 알루미늄 몸체가 전체적으로 손상되지 않았 음을 입증했습니다.
동시에, 알루미늄 차체의 장점에 대한 인식은 문제가되지 않습니다. 철강 차체 기관차 및 차량 제조업체는 독일의 얼음 열차 제조 공정에서 알루미늄에 중점을 둔 것에 대해 우려를 표명하고 1994 년에 철강의 우월성을 확인하기위한 연구를 수행했습니다. 그러나 이전과 마찬가지로 강철 구조물을 사용하면 차체의 중량이 약 20 % 증가합니다.
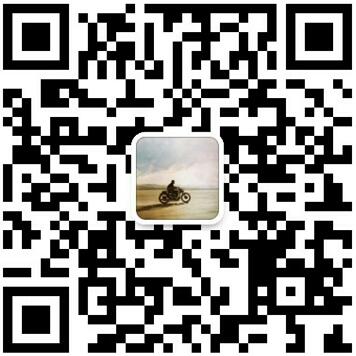
제품의 무료 제공, 언제든지 상담을 환영합니다, 우리는 첫 번째 회신을 줄 것이다. 우리의 이메일 :