
86 17344894490
service@chalcoaluminum.com
철도 차량용 알루미늄 벌집 패널
도시 철도 차량 제조 산업은 치열한 경쟁을 벌이고 있습니다. 에너지 절약 및 배출 감축은 산업의 미래 발전 방향입니다. 경량 디자인은 피할 수없는 추세입니다. 고강도 및 저밀도 재료의 적용은 항상 차량 설계 및 제조 탐사의 핫스팟이었습니다. 그 중 알루미늄 복합 재료 보드는 비교적 새로운 유형의 차체 제조 재료이며 샌드위치 구조는 구조 접착제로 압착 된 알루미늄 패널, 핵심 재료 및 알루미늄 패널로 만들어집니다.
철도 차량용 알루미늄 벌집 패널
Chalco Aluminum에 의해 생산 된 철도 차량 용 알루미늄 벌집 패널은 상단 커버 부분이 알루미늄 복합 재료 플레이트를 채택 한 후 무게가 1095kg에서 965kg으로 감소하고 중량 감소율이 12 %에 도달하며 중량 감소 효과가 분명합니다. 그러나 비교적 복잡한 구조와 표면 알루미늄 시트의 넓은 영역으로 인해 기존의 MIG 용접을 구현할 수 없으며 차체의 조립 및 밀봉은 일반적으로 레이저 용접 또는 리벳팅으로 완료됩니다.
알루미늄 벌집 패널 은 진공 열압착 본딩에 의해 형성된 상부 피부, 하부 피부, 하트 우드 및 가장자리 밴딩 프로파일로 구성된 "샌드위치"구조입니다. 그 중에서도 차체의 다른 부분의 위치에 따라 주변 가장자리 씰링 프로파일을 적절하게 조정할 수 있으며 중간 코어 재료를 다른 두께로 설계 할 수도 있습니다. 알루미늄 복합 재료 플레이트를 사용하는 알루미늄 합금 차체 구조는 일반적으로 차체 알루미늄 프로파일, 굽힘 부품 등으로 구성된 프레임이며, 복합 재료가 설치된 알루미늄 복합 재료 플레이트와 리벳 또는 레이저로 용접되어 차체를 형성합니다. 그 중에서도, 지붕의 큰 부분에 있는 알루미늄 복합재료 판의 구조는 도 1에 도시되어 있다. 상단 커버 만 알루미늄 복합 재료로 만들어졌으며 상단 커버의 무게가 1095kg에서 965kg으로 감소하고 상단 커버의 중량 감소가 12 %에 도달하고 중량 감소 효과가 매우 분명합니다.
알루미늄 벌집 패널의 적용은 도시 철도 차량의 무게를 효과적으로 줄일 수 있으며 알루미늄 합금 차체 경량 재료에 대한 새로운 선택을 제공 할 수 있습니다. 용접 - 리벳 팅 - 본딩 공정은 차체 제조를 결합하여 프레임의 조립 정확도와 용접 변형 제어에 대한 더 높은 요구 사항을 제시합니다.
알루미늄 합금 차체의 샌드 블라스팅, 프라이머 및 탑코트와 같은 페인팅 작업은 알루미늄 복합 재료 보드를 설치하기 전에 완료해야합니다. 과도한 온도는 알루미늄 복합 재료 보드 자체, 실란트 등의 노화로 쉽게 이어질 수 있으며, 심지어 고장, 차체의 수명 단축 등을 초래할 수 있습니다.
알루미늄 복합 플레이트와 프레임 사이의 실란트는 리벳 조인트의 방수 성능을 효과적으로 보장 할 수 있습니다. 차체의 수명과 같은 요인을 고려하여 수입 고무를 선호 할 수 있습니다.
리벳팅 공정은 알루미늄 복합 재료 플레이트의 알루미늄 합금 차체의 제조 요구 사항을 충족시킬 수 있습니다. 소규모 배치 생산의 경우 대형 배치 프로젝트, 자동 드릴링 및 리벳팅 생산 라인과 같은 수동 작업을 사용하여 작업 강도를 효과적으로 줄이고 생산 효율성을 향상 시키며 제품 품질을 보장 할 수 있습니다.
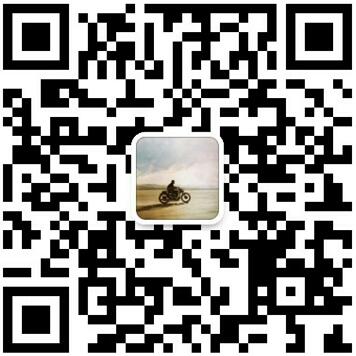
제품의 무료 제공, 언제든지 상담을 환영합니다, 우리는 첫 번째 회신을 줄 것이다. 우리의 이메일 :